BUILDING A
FOUNDATION
CREATION & INSTALLATION...
Creating in secret...
It was by pure luck that Shirley was engaged in doing a major commission for Mercy Medical Center in Cedar Rapids (later named Merging Rivers) when she was given the opportunity to do an artwork in honor of her husband Darrell Wyrick as he neared his retirement as CEO and President of the University of Iowa Foundation. In addition, this sculpture was to be a surprise for Darrell.
One might have thought that her working nonstop in her studio (that was attached to the Wyrick’s home) might have occasioned some curiosity in her husband about what she was doing as she was working in her studio every day for long periods of time.
But Darrell was deeply absorbed in overseeing the building of the Levitt Center for University Advancement--the Capstone to his career. Being detail-oriented (as was she) he went from floor-to-floor of the new building daily, noting what had been done that day and listing any concerns or problems to discuss the next day. He spent many hours conferring with the architect and the contractors and checking on details. In other words, he returned home exhausted, not really wanting to look into Shirley’s studio.
The foundry for “Building a Foundation”...
The artist had been working for some time with a small foundry in Osceola, Wisconsin to cast bronze sculptures. She relied on it to do a great job casting her artworks such as Building A Foundation and she cherishes having worked with them and also having learned even more about a more advanced casting process.
American Bronze Casting was founded by Wally Shoop, a wildlife artist. The business was run by his two sons, Wally, Jr. who is supervisor of the foundry, and John Shoop, its business manager. Wyrick saw that their care for detailed replication of artworks was perfect for her needs.
By the late 1990’s, Wyrick had grown to rely on the foundry when she wanted to have her smaller-scale sculptures cast into bronze. In addition to excellent craftsmanship, they were accurate in giving her fixed and reasonable costs prior to casting (something that some of the other small foundries she worked with had been unable to do!)
Making the Patterns...
The artist’s concepts for Building A Foundation are told in its brochure, but there were additional components to make the project even more challenging.
The curvature of the wall was the first major challenge. The design plan had to be checked for accuracy during construction. But at the time she needed to have the exact measurement for the curve, the inner part of the wall was up, but not as yet fleshed out. She was able to judge the depth of the wall well enough to be able to make the wood base for the plastilene clay reliefs.
The completed curved wood base supported a layer of Styrofoam and was topped by the plastilene for carving. The seven curved patterns then were lined up, two at a time, to judge whether a mostly seamless relief would be possible.
The design itself was of course challenging: interweaving strands of
DNA with well-known University of Iowa landmarks (ones that the UIF
had had a major part in finding funding) and more abstract images to complete the work. This is the part of the creative process that the artist loves the most!
The most nerve-racking time came just as the UI Foundation was preparing for the grand opening of the Levitt Center for University
Advancement. The finished castings had to be ready to be trucked back to Iowa City and the pieces had to be installed in one day before Darrell found out what was going on!
Renting a truck and loading it...
Osceola, Wisconsin is located straight east of the Twin Cities of Minnesota and is about a six-hour drive north from Iowa City. Wyrick had to deliver her patterns to the foundry and she often joked that given a little more instruction, she could use her truck-driving ability to land a “paying” job.
Wyrick first had to do the math to rent a truck with the capacity for patterns of the two sculptures, Merging Rivers and Building A Foundation , to lie flat on one level and make sure the weather was cool enough for the plastiline patterns. (On a previous trip in her van with another artwork, heat had threatened to melt her plastilene patterns being carried in the back of the van.)
Patterns for both Merging Rivers and Building A Foundation were loaded into the truck with help of friends and David Dennis, long-term head of exhibitions at the UI Art Museum, was among them. And when the finished castings were returned to the Levitt Center, David oversaw their installation.

At the foundry...
Wally Shoop, Jr., supervised the unloading of the patterns and directed the process of casting throughout.
The curvature of the pattern is evident as two of the foundry workers work on it. This photo shows a side view of the curved pattern.


The next stage of the “lost wax process” was to make PMC (Polyurethane Molding Compound) or “rubber molds” from the plastilene patterns.
Building A Foundation molds are secured with corner blocks: to keep the pattern from shifting. (In the scan below, the plastilene pattern for Merging Rivers lies beside those of Building A Foundation. Since Merging Rivers is flat, it did not require the exacting work that the curved patterns required.
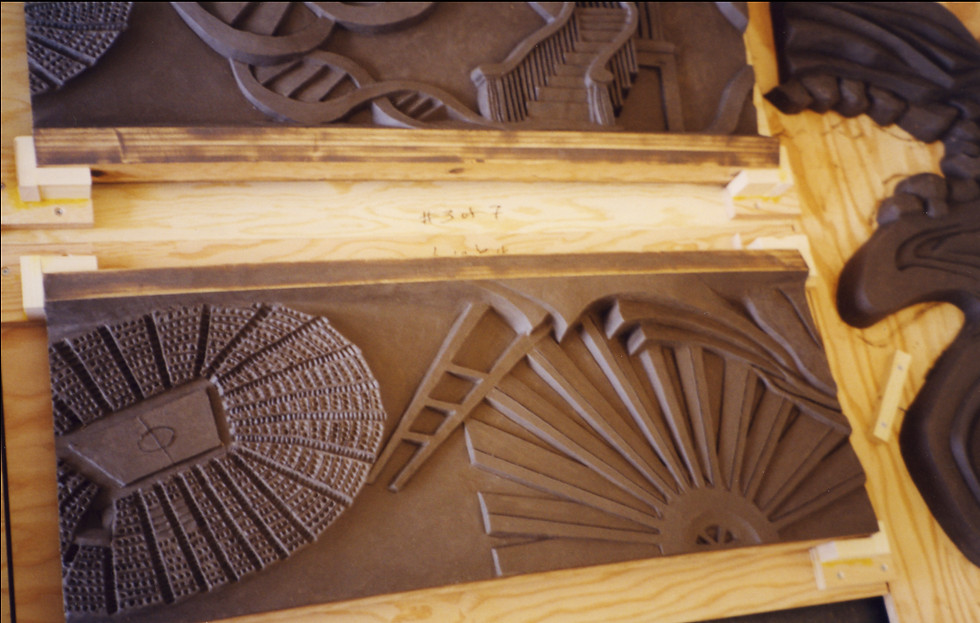
A few more views
of the plastilene patterns:



Shoop’s Photo Essay on
the Lost Wax Process of Bronze Casting...

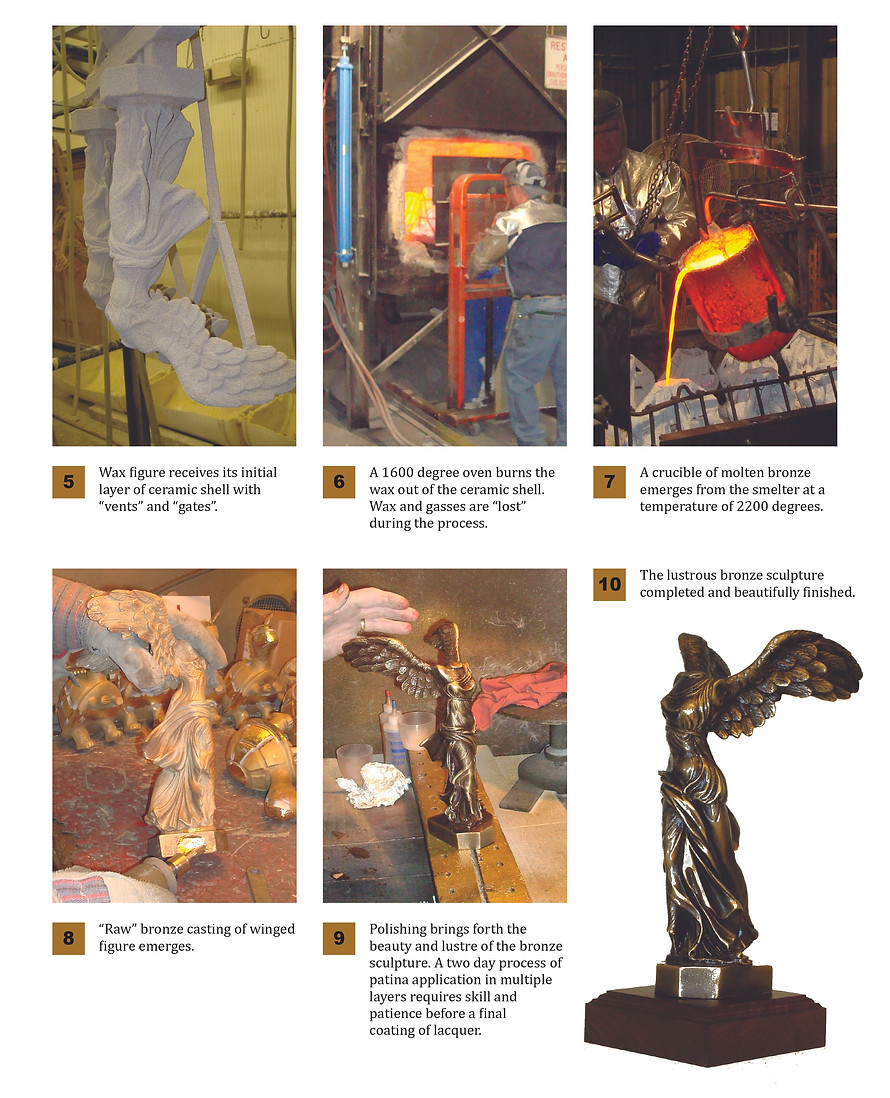
The artist is indebted to the Shoop’s American Bronze Casting, Ltd. for their permission to print their publication of the “Labor Intensive and Dynamic Lost Wax Process of Bronze Casting.”
Their process involves making PMC (polyurethane) molds (commonly called rubber molds) for each plastilene mold. The rest of the process is explained by the Shoop method and modified by the larger size of Wyrick’s plastilene molds.
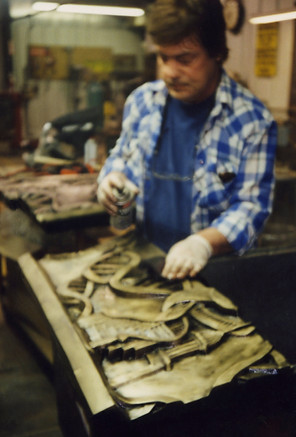
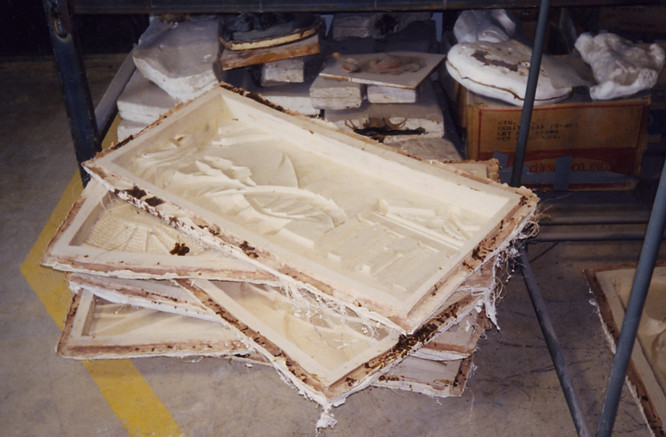
A “gravity fed system of pouring” was used at the ABC foundry. Outlets (or sprues) were provided to evacuate the wax as it melted out in the high heat of the furnace and the cavity left is filled with molten bronze, Wyrick’s earlier training in pouring bronze involved sand molds rather than the ceramic shell method and required two people to pour the molten bronze. It did not involve wax positives or ceramic shell. Wyrick found this lost wax method fascinating and she was always pleased by the result.
She was content to bring her sculptures to American Bronze Casting for its quality work.
Installation of
Building a Foundation in Secret...
Looking back, Shirley realizes what a miracle of timing took place in keeping the secret of this work from her husband. She was able to schedule the installation of the work two days before the presentation of the work to Darrell when he was occupied with more building inspection and meetings. Presentation to Darrell was also done just a day ahead of the formal opening of the building.
American Bronze Casting, faced with her deadline, came through and she drove a truck up to Wisconsin one day before installation, had it unloaded on the day of installation, and was able at the last minute to stop Darrell from going on his daily inspection tour on the 4th floor after the
installation of the sculpture had taken place. This was, of course, aided by the cooperation of his entire staff!
David Dennis helped move the pieces from the loading dock and with the aid of two assistants, installed the bronzes. Shirley was also on hand to help.

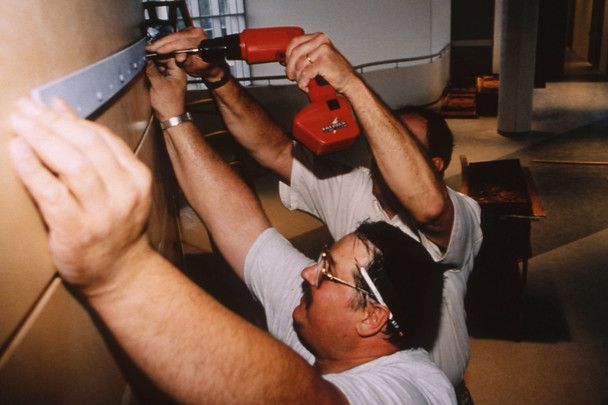
Installing the work went smoothly and matching the curve to the wall was successful.


The artist’s signature is on the right end of the sculpture; the name of the artwork is on the left end:
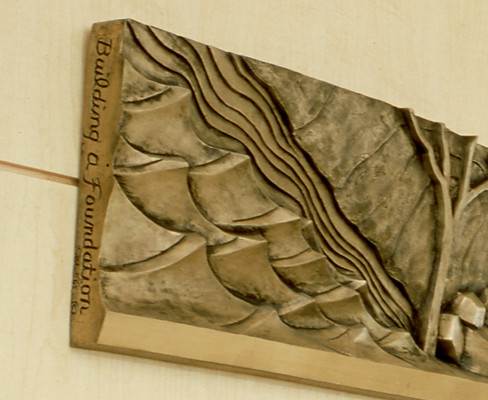

The UI Foundation staff assembled to surprise Darrell on the day after installation and he was indeed surprised! He recognized it as Shirley’s work but did wonder how he had been kept in the dark about it . . .


A Postscript...
In the early 1990’s, the UI Foundation headed by Wyrick’s husband Darrell since 1962, was able to think about a more permanent location for its offices that had most recently been housed in the UI Museum of Art. Due to a major gift from Dick and Jeanne Levitt, the Foundation was able to move forward on planning its own building.
The UI Foundation had occupied several spaces allotted to them by the University of Iowa, beginning in the Alumni House, an old house across from the Iowa Memorial Union. Its most recent officers were in the Museum of Art and it had weathered the Flood of 1993 by moving across the river to the new Technology Laboratory.
At that time the decision was made by the Foundation Board to build a building removed from the flood plain at 1 West Park Road to create a Center for University Advancement to house both the UI Foundation and the UI Alumni Association. This was to be the capstone to Darrell Wyrick's career, since he had overseen building the Foundation from a bootstrap operation in 1962 into a thriving institution through the force of his personality and the aid of his dedicated staff.
Della McGrath, the Foundation’s Director of Operation, Facilities and Project Management, felt it would be fitting if Darrell’s wife Shirley could be asked to create an artwork to honor her husband and she arranged a meeting between the New York architect for the building, Charles Gwathmey, and Shirley. After that meeting, Shirley proposed that she create bronze reliefs in the building, even suggesting that she might cover some of the many pillars in the building with bronze reliefs. That was not something Gwathmey endorsed, but he did agree with the artist on doing a bronze relief on the curved wall outside the Foundation’s Board Room on the 4th floor of the building.
McGrath raised the funds needed for the cost of producing Shirley’ work in a quiet campaign and Shirley gifted her creative time and labor for the project.
Another artist, Hu Hungshu, was selected to create the major artwork for the Levitt Center through the AISB (Art in State Buildings) initiative. (One half of one percent of any new State building’s cost is mandated by the State of Iowa to be allocated to Art.)
Hungshu’s work, “D Forever,” a four story work hanging in the Center’s Atrium, also serves as a tribute to Darrell.